Manufacturing 10,000 bottles at 96% Reduction in Cost Using 3D Printed Molds
In more than 200 countries, around 1 billion people enjoy Pepsi products that came from a 3D printed mold. Large Enterprises are saving Millions of Dollars every year on packaging production.
Sustainable and eco-friendly packaging has emerged as an end-to-end business solution and there are high possibilities for 3D printing in the sector. The manufacturing cycle of 3D printing packaging uses environmentally conscious materials or processes that result in a high-quality product that helps businesses attain corporate sustainability goals.
Benefits of 3D-Printed Packaging
With 3D printing technology, businesses can reduce the quantity of plastic in packaging designs without having to compromise on product quality. According to a study carried out by Michigan Technological University indicates that about 41% to 64% less energy is consumed to 3D print an item as compared to its counterpart process. In addition to this, even a small reduction in the packaging material used can result in a significant saving in costs for enterprises. Hence, 3D printing applications across industries result in significant cost savings and reduced production time. Additionally, including a sustainability aspect within a product also contributes to marketability when targeting particular customers and helping companies attain corporate sustainability goals.
Alongside the several environmental benefits of 3D-printed packaging, the scalability and design freedom offer corporations the hedge of prototyping designs before dealing with costly materials. Through this technology, brands can offer personalized packaging to their customers. A good example can be Marchesini, an Italian company producing a wide range of packaging for different industries, including cosmetics, pharmaceuticals, and food packaging.
Moreover, another considerable benefit is decentralized manufacturing which was highly evident during the COVID-19 pandemic as the entire global supply chain was disrupted and shipping was halted. By using 3D printing technology enterprises can swiftly move production sites as the system will rely on digital printed files in place of massive and immobile factories. Digital files also allow for on-demand 3D-printed packaging. For example, printing packaging orders quantity to as near as required, reducing waste and the volume of packaging that will eventually end up in a landfill. Furthermore, time-sensitive sales opportunities like Olympics can benefit from targeted limited-batch 3D-printed packaging with the reduced risk of over-producing.
PepsiCo hits the spot with 3D printing
In more than 200 countries, around 1 billion people enjoy Pepsi products on a daily basis. Having net sales of more than $79 billion in 2021, the beverage company considered speed to market to be the most challenging task as the brand aims to develop new bottle and package designs to address ever-shifting customer desires. However, creating of conventional metal tooling for blow molding of bottles is not only a time-consuming but an expensive proposition as well. An entire set can cost up to $10,000 to produce a single metal tool set, depending upon its level of complexity.

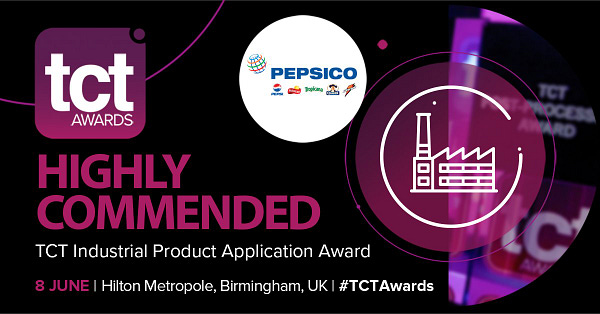
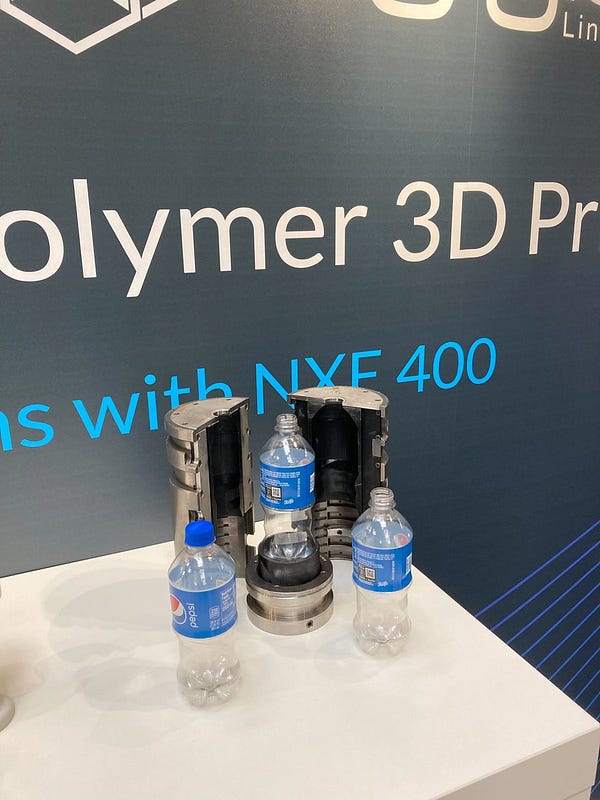
Application
Applying its patented technology, PepsiCo has entered into additive manufacturing serving to be an enabler in various aspects of bottle creation – advanced system analysis, accelerating and enhancing performance simulation, and producing high-quality and functional prototypes.
Advantages
Compressed prototype tooling development time from 4 weeks to 48 hours
Creating durable tooling that has the capacity to produce more than 10,000 bottles per mold
Slash prototype tooling that costs from $10,000 to $350 per mold set
Enabling multiple design iterations that allow timely verification of downstream activities
Manufacturing 10,000 bottles at 96% Reduction in Cost
Pepsi has incorporated Nexa3D’s xPEEK147 from Henkel Loctite for the 3D printed tool mainly due to material strength along with impressive performance factors, such as very high heat-deflection temperature. Although the hybrid approach is machine-agnostic, which means that it makes use of several types of 3D printers, PepsiCo has invested an ultrafast, high-throughput Nexa3D NXE 400 3D printer and associated material performance that serves to be an ideal for the production of mold components required.
A complete mold set is produced in 12 hours (8 hours of 3D printing time and 4 hours of curing). These hybrid-made molds can be used for more than 10,000 bottles before it being expired, this eventually results in 96% reduction in the cost in comparison to the conventional meta tooling way.
3D Printing for Eco-Friendly Containers By HP
Acquisition of Choose Packaging by HP is to make use of paper containers that can be used in place of packaging for laundry detergents, drinks, food and make-up. The highlight of the deal is the special plant-based barrier material that can make molded fiber containers to be waterproof. Moreover, the packages are recyclable and compostable as well.
Choose packaging relies on HP’s Multi Jet Fusion (MJF) 3D printing technology to fabricate the molds. The acquisition enhances the existing molded fiber tooling service. The 3D printing tool quickly makes molds that deliver both high-performing and less error-prone than conventional counterparts. These molds can be used for trays, egg cartons and packaging.
The company aims to take a leading position in the market with this acquisition, helping a specific vertical, tooling as a service to move a step ahead. This deal will also offer inexpensive, quick, high-performance molded fiber packages for various fast-moving consumer goods (FMCGs). By using molded fiber, the company will save 150 million tons of wasted plastic and interrupt the $10 billion fiber packaging industry, which is a great achievement.
L’Oréal in Additive Manufacturing
In 2018, the cosmetic giant initiated a digital transformation strategy which has also become the need of businesses today. The incorporation of 3D printing is used in making packaging prototypes, point-of-sale furniture prototypes, furniture prototypes, quality control tools prototype injection molds, and spare parts for the packaging line of the factory. 3D printing is used for conformal cooling in injection molds and occasionally for make-up powder compaction tools.
In terms of internal organization, the benefit of using these tools is that a product can be designed and tested for ergonomics, which was quite a hefty task previously. Several design assumptions and new features are added from which the most relevant ones are selected. Moreover, the internalization of manufacturing of format parts tooling allows the company to be much more agile.